The Ultimate Guide to Precision Plastic Injection Moulding
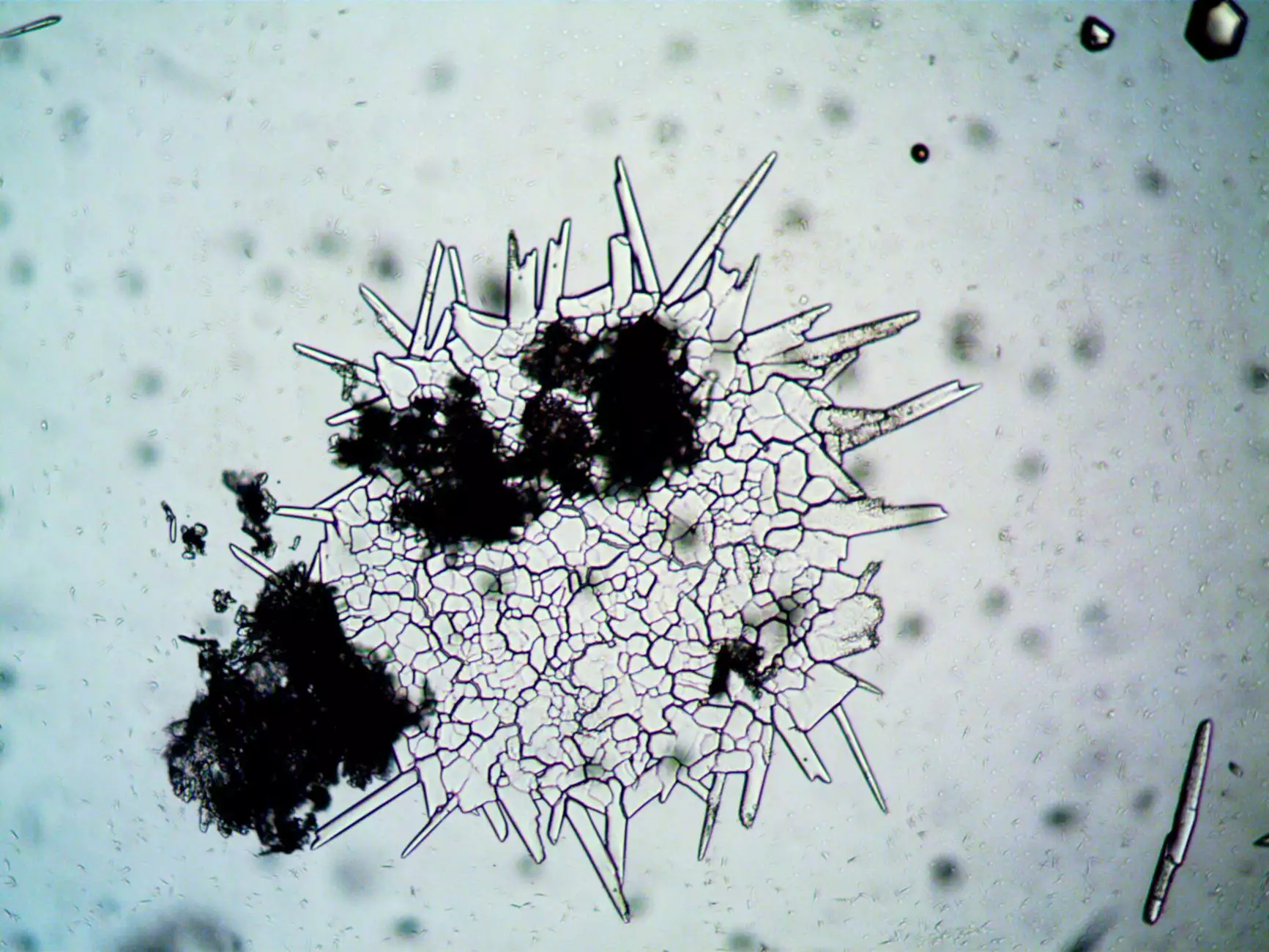
Precision plastic injection moulding is a revolutionary manufacturing process that has transformed the production of plastic parts across various industries. From automotive to electronics, this technique allows for the creation of complex and high-precision components at scale, meeting the increasing demands of modern technology and design. In this article, we will delve deep into the world of precision plastic injection moulding, examining its processes, benefits, applications, and future trends.
Understanding Precision Plastic Injection Moulding
At its core, precision plastic injection moulding involves injecting molten plastic into a mould to create parts that are highly accurate and can be replicated in large quantities. The process is lauded for its ability to produce intricate designs with tight tolerances, making it a preferred choice for manufacturers worldwide.
The Injection Moulding Process
The injection moulding process can be broken down into several key phases:
- Material Preparation: Plastic pellets are fed into the injection moulding machine and heated until they melt.
- Injection: The molten plastic is injected under pressure into a mould cavity.
- Cooling: The plastic cools and solidifies inside the mould, taking on the shape of the cavity.
- Demoulding: Once cooled, the part is ejected from the mould.
- Finishing: Additional processes such as trimming or surface finishing may be applied to achieve the desired look.
Benefits of Precision Plastic Injection Moulding
Choosing precision plastic injection moulding for manufacturing offers numerous advantages:
- High Precision: This method provides exceptional accuracy, crucial for parts that must fit together perfectly.
- Cost-Effective for Large Volumes: Once the mould is created, per-part costs decrease significantly when producing in large quantities.
- Versatility: This process can accommodate a wide range of materials, including various types of plastics such as thermoplastics and thermosetting plastics.
- Complex Geometries: Designers are not limited by simple shapes; almost any shape can be achieved with proper mould design.
- Reduced Waste: The injection moulding process is efficient, resulting in minimal material waste compared with other manufacturing methods.
Applications of Precision Plastic Injection Moulding
The versatility of precision plastic injection moulding allows it to serve multiple industries, including:
- Automotive: Parts such as bumpers, dashboards, and interior components.
- Consumer Electronics: Casings, buttons, and connectors for devices like smartphones and laptops.
- Medical Devices: Syringes, casings, and components that require sterile manufacturing processes.
- Toys: Safe, durable, and precisely manufactured toys for children.
- Household Goods: Kitchenware, storage containers, and various everyday items.
Key Players in Precision Plastic Injection Moulding
Within the industry, several key players stand out for their innovative approaches and high-quality outputs in precision plastic injection moulding. Companies often employ state-of-the-art technology to push the boundaries of what is possible in manufacturing. One notable example is Deep Mould, a leader in the field of precision plastic moulding.
Innovations in Mould Design
Advancements in technology have led to significant improvements in mould design. Computer-aided design (CAD) software allows for the creation of intricate moulds with precise specifications. Additionally, additive manufacturing (3D printing) is increasingly utilized to produce moulds more quickly and efficiently, allowing for rapid prototyping and testing.
Future Trends in Precision Plastic Injection Moulding
The future of precision plastic injection moulding is bright, with emerging trends that may redefine manufacturing processes:
Industry 4.0 and Automation
The integration of IoT (Internet of Things) and automation technologies into the production line enhances efficiency. Smart machinery can monitor processes in real-time, leading to fewer errors and reduced downtime.
Sustainable Practices
There is a growing demand for sustainable manufacturing practices. The industry is moving towards using biodegradable plastics and recycling materials to create new products. This approach not only meets consumer demand for eco-friendly solutions but also helps reduce the environmental impact of plastic waste.
Conclusion
In conclusion, precision plastic injection moulding is a crucial manufacturing process that has enabled the production of high-quality, precise components in a variety of industries. Its benefits, versatility, and continuous innovations make it a go-to solution for manufacturers looking to deliver exceptional products while optimizing efficiency.
Explore More About Precision Plastic Injection Moulding
If you want to learn more about precision plastic injection moulding and how it can benefit your business, consider reaching out to experts in the field, such as those at Deep Mould. They can provide insights into the latest technologies and applications in the precision moulding industry.